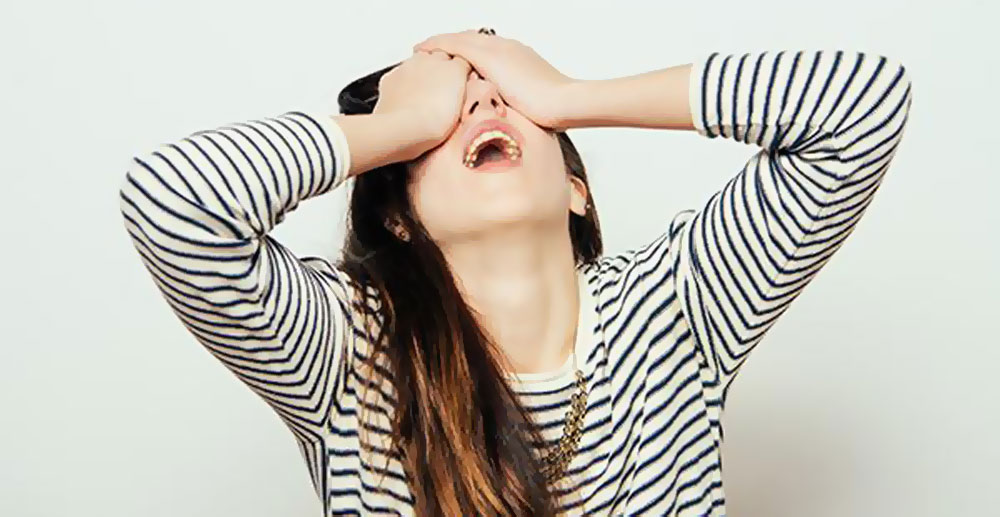
Three issues that create stress, loss of productivity and income are:
- Aged or Inferior equipment.
- Limited back up of Clipper Blades & Shears
- Turnaround time for sharpening
These three issues can reduce efficiency & profit by 20% to 50%.
1. Aged or inferior equipment
- Poor quality blades & shears will not hold a sharp edge for long.
- Money invested for re-sharpening may not be worth it.
- Our blades can be re sharpened at least 15-20 times and will run cooler for longer.
- Our shears are minimum 440C Japanese Stainless Steel providing longevity.
Best Practice – Have a critical look at your blades & shears and retire the ones that are not performing.
2. Limited number back up of Clipper Blades & Shears.
You need a minimum of three sets of each blade you use and the same with shears.
- One is away being sharpened.
- The second one dies or gets dropped – that’s two down!
- The third one keeps you going without stress & downtime.
Best Practice – List all blades & shears you use. Ensure you always have a minimum of three on hand.
3. Turnaround time for sharpening
- Our turnaround time is around 3 days from receiving your equipment. After test cutting, we Express Post to you.
- Its not uncommon for sharpening in Australia to take anywhere from 3 days to 4 weeks.
- If you do not have adequate back equipment up in your arsenal you cannot work efficiently.
Best Practice – Ensure your preferred sharpener can give you an approximate turnaround time before you send your equipment for sharpening – You may need more than three backups!!
Note: These best practice strategies will “Reduce Stress & Increase Profit”
Or call Wayne on 0407 000 466
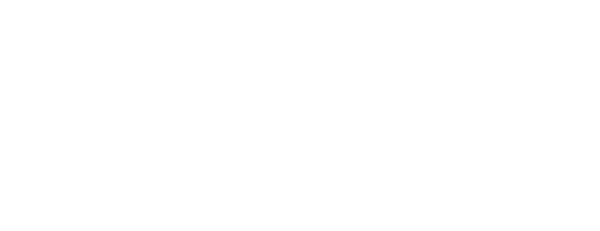